راههای کاهش مصرف انرژی در کمپرسورهای صنعتی
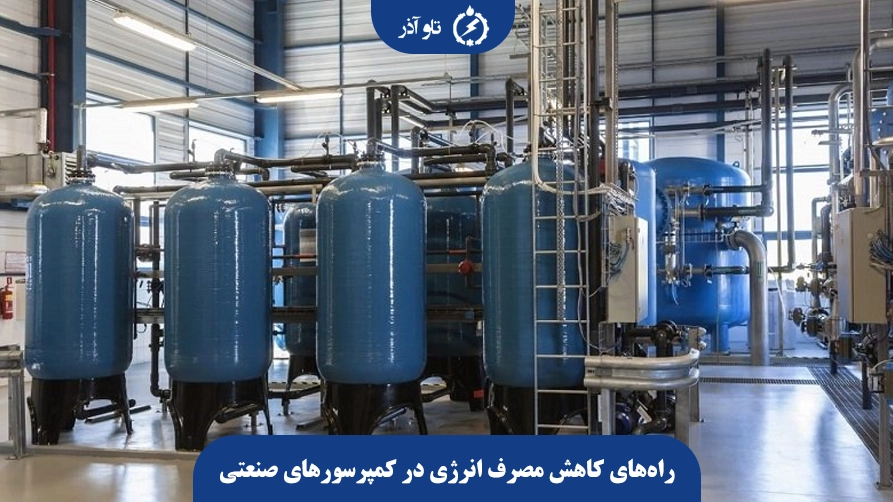
راههای کاهش مصرف انرژی در کمپرسورهای صنعتی
راههای کاهش مصرف انرژی در کمپرسورهای صنعتی در دنیای امروز، صرفهجویی در مصرف انرژی تنها یک انتخاب هوشمندانه نیست؛ بلکه یک ضرورت اقتصادی و زیستمحیطی است. کمپرسورهای صنعتی، بهعنوان قلب تپنده بسیاری از فرآیندهای تولید، یکی از پرمصرفترین تجهیزات کارخانهها و کارگاهها هستند. اما خبر خوب این است: با مدیریت صحیح و استفاده از تکنولوژیهای بهروز، میتوان مصرف انرژی کمپرسورها را به طرز چشمگیری کاهش داد. در این مقاله جامع، به بررسی عملیترین، فنیترین و موثرترین روشهای کاهش مصرف انرژی در کمپرسورهای صنعتی میپردازیم.
1. اهمیت کاهش مصرف انرژی در کمپرسورهای صنعتی
کمپرسورها بهطور میانگین 10 تا 15 درصد از کل انرژی مصرفی یک کارخانه را به خود اختصاص میدهند. در برخی صنایع این عدد به بیش از ۳۰ درصد نیز میرسد. این یعنی کوچکترین تغییر در بهرهوری، تأثیر بزرگی در کاهش هزینههای انرژی خواهد داشت.
علاوه بر کاهش هزینهها، بهینهسازی مصرف انرژی در کمپرسورها:
باعث کاهش انتشار گازهای گلخانهای میشود.
عمر تجهیزات را افزایش میدهد.
بازده کلی سیستم را بالا میبرد.
2. بررسی علل اصلی مصرف بالای انرژی در کمپرسورها
برای کاهش مصرف انرژی، ابتدا باید عوامل مصرف بالا را شناخت. مهمترین آنها عبارتاند از:
- انتخاب نادرست ظرفیت کمپرسور
- عدم استفاده از درایوهای دور متغیر
- نشتی در خطوط لوله یا اتصالات
- عملکرد نادرست سیستم کنترل
- نگهداری ضعیف و فیلترهای کثیف
- تنظیم فشار بیش از نیاز واقعی
3. راهکارهای عملی کاهش مصرف انرژی
یکی از مهمترین تصمیمها در صرفهجویی انرژی، انتخاب کمپرسور مناسب برای نیاز واقعی تولید است. کمپرسور صنعتی بزرگتر از نیاز باعث اتلاف انرژی شده و کوچکترها نیز دائم در حالت Overload قرار میگیرند.
نکته حرفهای: پیش از خرید کمپرسور، یک تحلیل دقیق از الگوی مصرف هوای فشرده در بازههای زمانی مختلف انجام دهید.
استفاده از اینورتر (VSD – Variable Speed Drive)
اینورتر یا درایو دور متغیر، امکان تنظیم دور موتور بر اساس نیاز واقعی به هوای فشرده را فراهم میکند. این باعث میشود موتور تنها بهاندازه مورد نیاز کار کند و از خاموش/روشن شدن مداوم جلوگیری شود.
مزایا:
- کاهش 30 تا 50 درصدی مصرف انرژی در برخی شرایط
- افزایش عمر موتور و تجهیزات
- کاهش صدای عملکرد کمپرسور
تعمیر و نگهداری منظم
نگهداری پیشگیرانه کلید بهرهوری در سیستمهای کمپرسور است. فیلترهای کثیف، روغن آلوده یا تسمههای فرسوده باعث میشوند کمپرسور با راندمان پایینتری کار کند.
برنامهریزی منظم شامل:
- تعویض روغن در بازه زمانی توصیه شده
- بازبینی منظم فیلترهای هوا، روغن و جداکننده
- کنترل عملکرد شیرها و سنسورها
- بررسی نشتی و فشار خط
کاهش نشتی هوا
نشتی در سیستم هوای فشرده میتواند تا ۳۰ درصد هوای تولیدشده را هدر دهد. معمولاً این نشتیها در اتصالات، شیرها، شیلنگها و کوپلینگها رخ میدهد.
راهکارها:
- استفاده از دستگاههای التراسونیک برای شناسایی نشتی
- آموزش پرسنل برای تشخیص و گزارش سریع نشتی
- ثبت و گزارشگیری منظم برای کاهش اتلافات
بهینهسازی سیستم لولهکشی
طراحی ضعیف لولهکشی موجب افت فشار و هدررفت انرژی میشود. مسیرهای طولانی، انشعابهای زیاد و قطر نامناسب لولهها همگی در این کاهش راندمان نقش دارند.
راهکارهای بهینهسازی:
- کاهش تعداد زانویی و شیرهای غیرضروری
- استفاده از لولههای با سطح داخلی صاف
- رعایت شیب مناسب برای جلوگیری از تجمع رطوبت
ذخیرهسازی هوای فشرده با مخازن مناسب
مخازن هوای فشرده باعث کاهش تعداد دفعات روشن و خاموش شدن کمپرسور میشوند و کمک میکنند تا در زمان پیک مصرف، فشار سیستم افت نکند.
ویژگیهای مخازن مناسب:
- حجم مناسب با توجه به ظرفیت کمپرسور
- نصب در نقاط کلیدی نزدیک به مصرفکنندههای عمده
- تجهیز به شیر اطمینان و شیر تخلیه اتوماتیک رطوبت
استفاده از سیستمهای بازیابی حرارت
تا 90 درصد انرژی مصرفی کمپرسور بهصورت گرما تلف میشود. با استفاده از سیستمهای بازیابی حرارت، میتوان این گرما را برای گرم کردن آب، هوای محیط یا فرآیندهای صنعتی دیگر بازیافت کرد.
کاربردها:
- پیشگرمایش آب بویلر
- گرمایش سالنهای تولید در فصل سرد
- کاهش نیاز به هیترهای الکتریکی
4. نقش اتوماسیون و مانیتورینگ هوشمند
اتوماسیون صنعتی و سیستمهای مانیتورینگ، امکان پایش لحظهای وضعیت کمپرسورها و تحلیل دادهها را فراهم میکنند. این اطلاعات کمک میکنند تا نقاط ضعف سریعتر شناسایی شده و اقدامات اصلاحی بهموقع انجام شوند.
سیستمهای هوشمند شامل:
- مانیتورینگ فشار، دما و رطوبت
- ثبت نمودار مصرف انرژی
- هشدارهای نگهداری و بهرهبرداری
- اتصال به سیستمهای مدیریت انرژی کارخانه (EMS)
5. آموزش کارکنان و تغییر فرهنگ مصرف
در نهایت، تکنولوژی بدون آگاهی نمیتواند بهرهوری را افزایش دهد. آموزش اپراتورها و کارکنان کلید استفاده صحیح از تجهیزات است.
موارد آموزشی پیشنهادی:
- نحوه تشخیص نشتی و گزارش آن
- عملکرد بهینه کمپرسورها و سیستم هوای فشرده
- رعایت اصول خاموشکردن صحیح در ساعات بیکاری
- اهمیت فیلترها، روغن و فشار بهینه
6. نتیجهگیری و جمعبندی
کاهش مصرف انرژی در کمپرسور صنعتی یک هدف دستیافتنی است که با ترکیبی از تجهیزات مناسب، نگهداری اصولی، اتوماسیون و فرهنگسازی میتوان به آن رسید. سرمایهگذاری در این حوزه نهتنها هزینههای جاری را کاهش میدهد، بلکه بهعنوان یک قدم مؤثر در مسیر توسعه پایدار نیز محسوب میشود.
با توجه به سهم بالای کمپرسورها در مصرف انرژی صنایع، نادیدهگرفتن این حوزه به معنای پذیرش هزینههای پنهان و کاهش رقابتپذیری خواهد بود. پس بیایید با تصمیمگیریهای هوشمندانه و علمی، آیندهای روشنتر و اقتصادیتر برای صنعت بسازیم.
گامهای عملی برای شروع مسیر بهینهسازی مصرف انرژی
اگر قصد دارید همین امروز قدمی در جهت کاهش مصرف انرژی کمپرسورهای صنعتی خود بردارید، این چهار مرحله را مدنظر قرار دهید:
ارزیابی وضعیت موجود:
مصرف انرژی سیستم کمپرسور را در حالت فعلی با ابزارهای اندازهگیری دقیق یا با کمک مشاوران متخصص آنالیز کنید. نقاط ضعف و گلوگاهها را شناسایی کنید.
تعیین اهداف مشخص:
مثلاً کاهش ۲۰ درصدی مصرف انرژی طی یک سال. راههای کاهش مصرف انرژی در کمپرسورهای صنعتی هدف مشخص، فرآیند تصمیمگیری و تخصیص بودجه را بسیار سادهتر خواهد کرد.
برنامهریزی و اجرای تغییرات:
بر اساس نتایج ارزیابی، اقداماتی مانند تعمیر نشتیها، نصب اینورتر، راههای کاهش مصرف انرژی در کمپرسورهای صنعتی جایگزینی کمپرسورهای قدیمی یا بهبود سیستم لولهکشی را اجرا کنید.
پایش و بهبود مستمر:
انرژی، یک پارامتر دینامیک است. شرایط کاری، تولید، دما و رطوبت تغییر میکند. پس سیستم پایش مداوم و بازبینی دورهای را در برنامههای خود بگنجانید.
تاثیر کاهش مصرف انرژی در آینده صنعت
روند جهانی به سمت «کارخانههای سبز» و «صنایع پایدار» در حال حرکت است. بسیاری از خریداران بینالمللی، میزان بهرهوری انرژی را یکی از ملاکهای ارزیابی تأمینکنندگان خود قرار میدهند.
کاهش مصرف انرژی در سیستمهای کمپرسور صنعتی میتواند:
- امکان دریافت گواهینامههای بینالمللی مانند ISO 50001 را فراهم کند.
- ارزش برند شما را در بازارهای داخلی و خارجی افزایش دهد.
- هزینههای تولید را کاهش داده و قیمت نهایی محصول را رقابتیتر کند.
حرف آخر
مدیریت مصرف انرژی فقط کاهش هزینه نیست؛ یک استراتژی بلندمدت برای توسعه پایدار و رقابت در بازارهای جهانی است. کمپرسورهای صنعتی با مدیریت هوشمندانه میتوانند به جای یک نقطه ضعف پرهزینه، به یک مزیت رقابتی ارزشمند تبدیل شوند.
پس اگر میخواهید هم در هزینههای امروز صرفهجویی کنید و هم آینده کسبوکار خود را بیمه کنید، کاهش مصرف انرژی در کمپرسورهای صنعتی باید همین امروز در اولویت برنامههای شما قرار گیرد.